
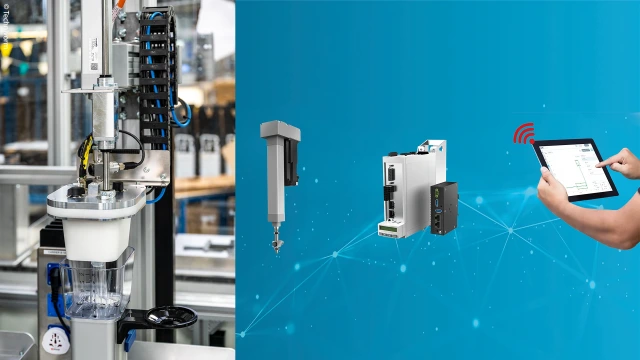
“Life is too short to drink bad coffee.” On the basis of this philosophy, Gerard Smit established the company Technivorm in 1964 and invented the well-known Moccamaster coffee machine. To ensure the perfect coffee, the Dutch manufacturer uses a new test line which was automated by Bosch Rexroth and its Certified Excellence Partner Rimas Technology.
Lower costs, greater output, higher availability – these were the requirements Technivorm placed on the new Moccamaster test line which tests a range of things including the water tank's leak tightness or the insulation for the lamps' and knobs' circuits. Automating the final approval process helps to reduce both costs and errors while increasing output.
The Smart Function Kit Pressing combines mechatronic standard components with intuitive operating software for quick commissioning, graphical sequencing, straightforward line integration and integrated process data collection. (Copyright: Bosch Rexroth)
The flexible aluminum profile kit from Bosch Rexroth forms the basis of the automation solution. It centers around the Smart Function Kit Pressing, an intelligent complete solution for pressing and joining applications which combines an electromechanical cylinder with a motor, drive, force sensor and industrial PC. Commissioning is easy: The pre-installed operating software guides users intuitively through the commissioning process in just a few minutes. Programming-free sequence creation using graphical modules helps to save even more time and visual sequencing makes it easier to adjust processes later on.
For the final check, the specific machine types must be tested with individual parameters. The Smart Function Kit Pressing receives the type-specific test parameters, e.g. the testing pressure to be used, from the line control system after scanning the product barcode. Thanks to the automated procedure, the process is now much quicker and the output has increased.
Another benefit of the Smart Function Kit: The process monitoring feature included in the software package can monitor and log the entire testing process. This enables Technivorm to check the possible cause of a fault using the documentation if a product is returned. Because the Smart Function Kit stores all test data on the system, the condition of each machine is known when it leaves the factory, making the handling of return and repair processes smarter and more efficient.
Technivorm is very happy with the automated test line. There are now fewer errors, testing costs have been reduced and output has increased. The new data collection feature also allows a detailed insight into production so that errors or faults can be analyzed and rectified more quickly. Ultimately, this ensures that customers get a perfect coffee machine – for the perfect cup of coffee, just as Technivorm founder Smit would have wanted.
Experience the Smart Function Kit Pressing in a video: