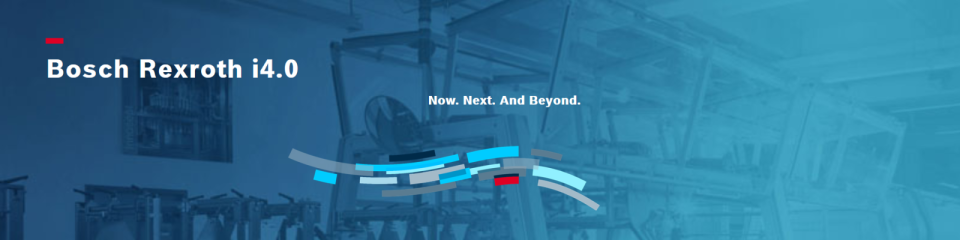
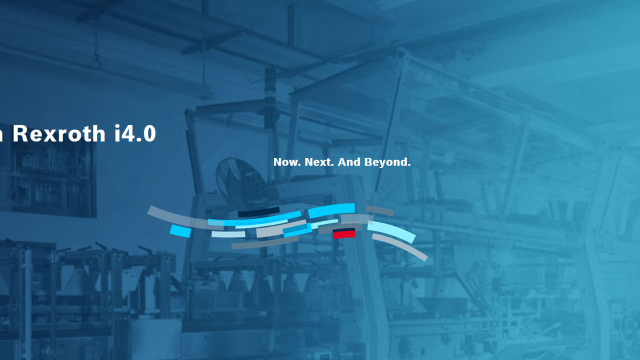
See how Sugar Creek Brewery increased efficiencies by implementing IoT technology in their craft brewery.
Situation Overview
Craft breweries are a booming business in the US, and with the Charlotte area boasting nearly 50 independent craft breweries, it's become a mini mecca for craft brew connoisseurs. With a rebellious spirit and passion for infusing traditional recipes with modern flavors and techniques, Sugar Creek Brewing Company, founded in 2014, specializes in crafting rich and aromatic Belgian style ales in the tradition of Belgian Trappist monks. Today, the company produces about 7,000 barrels a year and by adding a bottling operation, Sugar Creek has expanded sales to reach the greater CarolinasBottling beer is not without its challenges, however. The beer making process is more complex than people realize. For example, as beer moves from tank to tank along the bottling line, even a slight variation in pressure or temperature will create foam. Foam creates spillage, and spillage equals waste. In Sugar Creek's case, that beer spillage equated to $30,000 a month in lost revenue, making the case for a significant capital investment in technology. Deciding to implement Artificial Intelligence and Internet of Things (IoT) technology into their brewing process, Sugar Creek Brewing Company was poised to become a brewing factory of the future. To help facilitate the transformation, they turned to the Industry 4.0 experts at Bosch Rexroth.
We chose to partner with Bosch Rexroth for three reasons, says Sugar Creek's CEO and Co-founder, Joe Vogelbacher. For one, their brand is synonymous with quality. Their parent company, Bosch, has extensive experience in all types of manufacturing. And they are a leader in connected industry. This combination of experience and expertise made them the ideal partner for Sugar Creek.
A Phased Approach to Automated Bottling
Phase One
The first order of business was to make the entire bottling operation more transparent. Sugar Creek's team needed to be able to visualize the bottling process in real time from anywhere in the brewery, so that immediate action could be taken to correct issues when and where they were happening. Leveraging the extensive connected industry engineering experience of Rexroth, IoT sensors were installed in the beer tanks to monitor and report information on fill levels and temperature. That information was then transferred via Rexroth's IoT Gateway for analysis and visualization that operators could access in real time via laptop, tablet or mobile phone. With that information at their fingertips, operators can respond in real-time to adjust the temperature set-point remotely.
Phase Two
When the initial implementation proves successful, Sugar Creek is expanding the control and analytics functions to a total of 17 of their brewing tanks and adding the ability to remotely control their glycol tank level and boiler on/off function.
Results
As a result of this connectivity and visualization, Sugar Creek Brewing Company was able to save $120,000 last yearâmoney they could then reinvest into their business. And now that the company can monitor fill times, temperature, pH, gravity, pressure, carbonation and fill levels in real timeâthey're able to develop new processes and refine existing ones, so that in addition to waste reduction, they can increase efficiencies, manufacture more product, and improve the flavor and quality of their products.
Featured Solutions