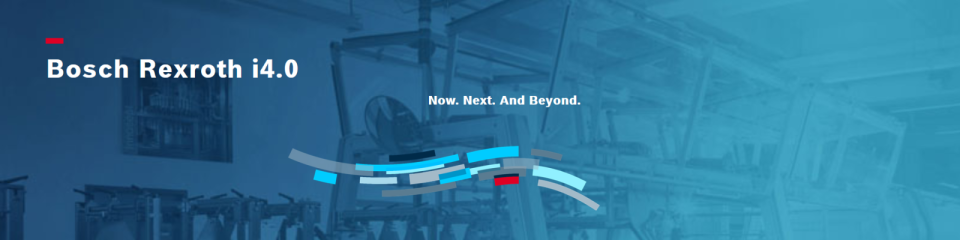
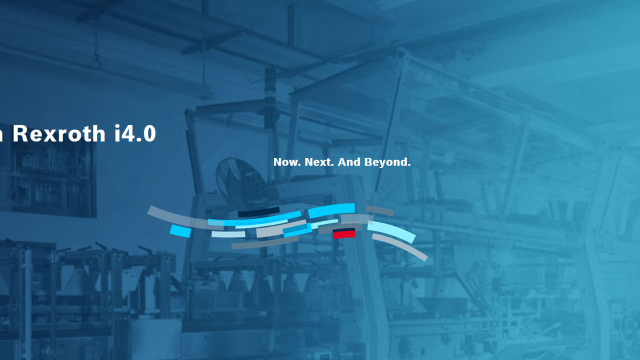
Author: Bosch Rexroth | September 30, 2019
The manufacturing industry is changing faster than ever before. As consumers demand more variety, manufacturers have to adapt, producing more product variations in the same amount of time and space, in order to stay profitable. Gone are the days of set-it-and-forget it; the successful factory of the future is a puzzle with infinite combinations. And while the fully connected Factory of the Future is attainable, even the most innovative and optimistic companies should not expect the pieces to come together all at once.
Rexroth understands this better than any Industry 4.0 solutions provider, because we have our very own proving grounds, putting our own i4.0 technology to work in hundreds of Bosch plants and warehouses all over the world, every day. Because we have implemented i4.0 solutions for ourselves, step by step - we can show our customers how do the same.
In a perfect (albeit magical) world, you could simply hit the pause button on your current factory and, from the ground up, build a fully connected, modular, internet-enabled smart factory in its place, without missing a beat. In the real world, however, we have to keep our factories running profitably today, while we solve for the demands of tomorrow. That means companies have to define their goals practically, in terms of specific use cases, and develop a roadmap that takes current operations into account.
"Many companies still see 'The Factory of the Future' as something they're going to have to embrace eventually, in order to stay relevant," says Rodney Rusk, head of Rexroth's Industry 4.0 Solutions group. "I challenge them to shift that mindset and ask, simply, what technology can I implement to improve my factory today that will also make me better positioned for tomorrow?"
"The answer to that question will differ from one manufacturer to the next," Rusk continues. "And some companies are already further along in their Factory of the Future journey than others. That's okay. It's still a matter of steps. No one is obligated to swallow the whole elephant."
While there are many steps along the way to the fully connected factory - there are some key milestones that will help you identify where you are and how to begin. Take an assembly plant for example:
1: Lean Principles
If you're a lean operation, you likely know it. You've implemented digital record keeping. Your internal communication is quick and transparent. You have taken steps to eliminate the physical impact of production work to reduce operator strain and minimize product scrap and project rework. You test and learn and are an organization committed to continuous improvement. If you still have some work to do in the lean arena - Bosch Rexroth has product-based solutions that can easily plug in to effect meaningful change. Lightweight, adjustable workstations are an easy and ergonomic substitute the steel stationary workstations of the past.
"No one understands continuous improvement better than Bosch," says Rusk. "This has been a systematic part of our organizational culture for decades."
2: Technology Integration
Once you've tackled the efficiency of your physical environment and assembly process, it's a natural progression to upgrade workstation technology. Digital supervision and direction tools prevent common assembly line errors and local sensors capture real time data to support more informed decision making. What's important is to implement open, scalable and flexible protocols that ensure your current state of multiple technologies can be integrated into your future state and won't hold you back.
3: Data Collection
Now that you have sensors in place, monitoring performance in real time, where does all that data go? For most manufacturers, the capital expense and downtime required to implement all-new technology for data collection is prohibitive. And with the rapid rate of innovation it makes far more sense to connect your existing machines and systems to an external network via an edge device like Rexroth's IoT Gateway. With embedded control hardware and installed open software, the IoT Gateway allows you to collect and analyze production and machine data without changing your existing machine programs.
4: Data Analysis & Visualization
Once you've decided what data you need to make fast, informed decisions, you need to display it in a way thatâs easy to interpret - and easy to access. "At the beginning of every shift," explains Rusk, "teams at Bosch will assemble to review data from the night before and identify any issues that require action. Before i4.0, we had to pull this data manually, organize it and tack it up on whiteboards. Whatever solution we devised would also have to be manually acted out, burning hours of time and resources. Now, with tools like Nexeed PPM, which pulls key data from the cloud or an edge device (like IoT Gateway), the analysis is completed in seconds, and the results are visualized in real-time on Rexroth's ActiveCockpit. The entire process is digitized, relieving the burden on workers, so they can focus on the job at hand."
5: Machine Learning
Manufacturers want maximum productivity and flexibility at minimum operating costs. Cabinet-free technologies, such as Rexroth's IndraDrive Mi , not only allow machines to connect to each other without wires and cables - they enhance information sharing to improve overall equipment effectiveness (OEE). These Smart Systems bring a whole new level of flexibility to the factory floor. Integrated drives and controls, independent pallet motion, and built-in safety sensors make way for a flexible factory in which only the walls, roof and floor are fixed. Connected devices can speak to each other, combining their tasks into a logical automated sequence. When your team no longer has to tell the machines what to do - they can focus on optimizing processes and creating new solutions.
6: Artificial Intelligence
The ultimate achievement in connectivity - and the largest return on investment - happens when machines can predict their own futures, flagging potential issues before downtime occurs. AI systems collect and analyze vast amounts of data in real time and perform predictive maintenance, reducing downtime and unnecessary repairs so machines operate as efficiently and effectively as possible.
Whether you're implementing manual solutions, looking to add modular technology, or are ready to implement full i4.0 connectivity in your factory, we're here to guide you. The steps are many, and our job is to make them manageable - meeting you and your organization where you are. If you'd like to discuss your roadmap, or need help defining one, contact Rodney or any member of the i4.0 team at Bosch Rexroth at i4.0@boschrexroth-us.com .